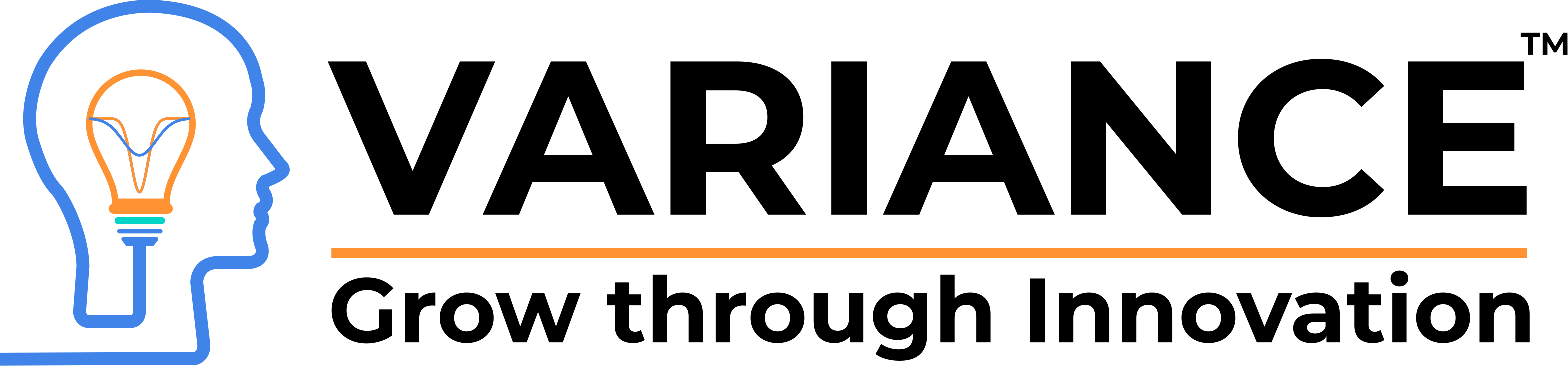
Pioneer in Offering CRM Solutions since 2010...
Variance InfoTech Pvt Ltd.
608/609, 6th floor - Abhishree Adroit,
Vastrapur, Ahmedabad, 380015, India
Phone : +91-7016851729
Email : info@varianceinfotech.in
Variance InfoTech LLC
30 N Gould St. Sheridan,
WY 82801 USA
Phone : +16305340223
Email : info@varianceinfotech.in
©Copyright 2025. All Rights Reserved | Privacy Policy
We use cookies to provide better experience on our website. By continuing to use our site, you accept our Cookies and Privacy Policy.
Accept